Leveraging Accurate, Actionable Data for Condition Monitoring Success!
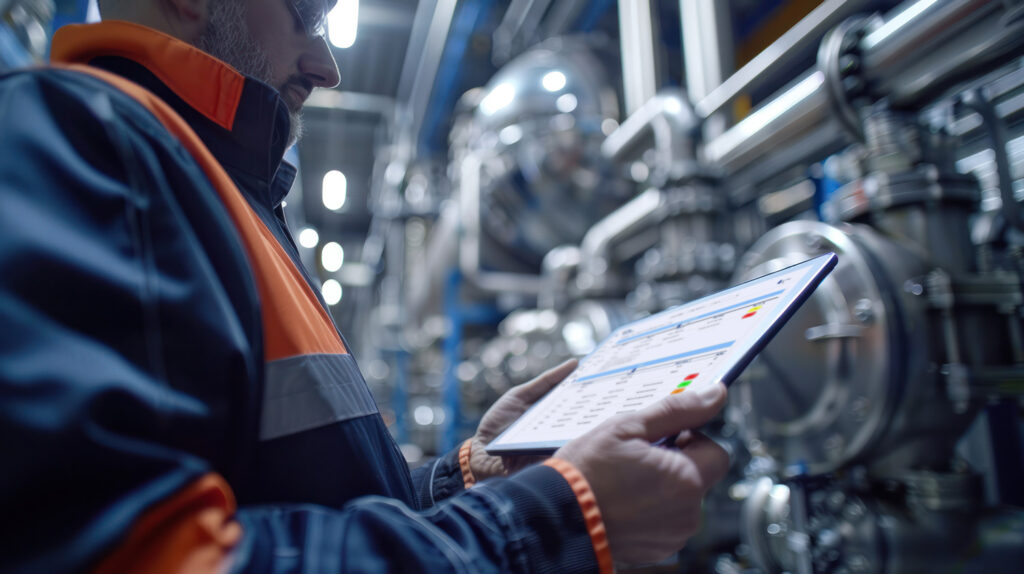
Our team recently returned from IR/INFO — the world’s premier infrared thermography conference. The hotel was buzzing with consultants, independent thermographers, and reliability engineers.
Are wireless ultrasonic sensors the future of condition monitoring for machine health?
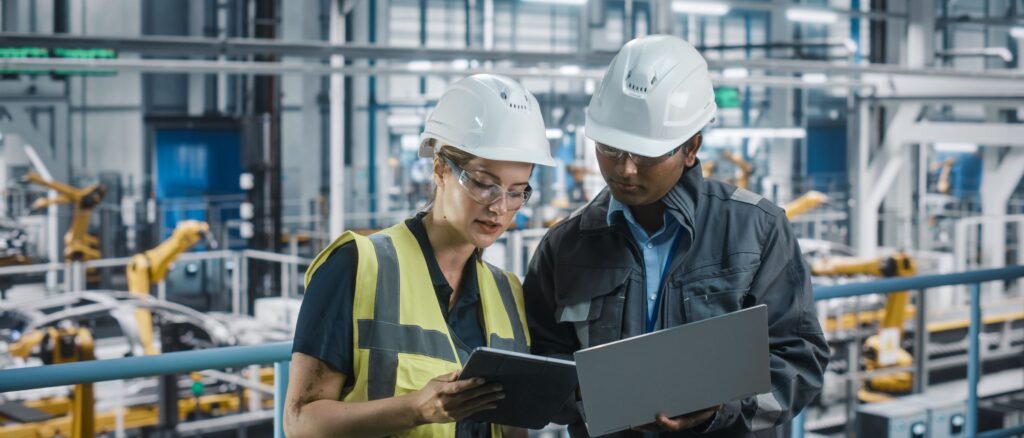
In today’s fast-paced manufacturing landscape, where optimizing equipment performance and minimizing downtime are crucial for staying competitive, ultrasonic sensors have become a critical component of the ultrasound condition monitoring industry. As a result, this industry has emerged as a pivotal early-detection strategy for predictive maintenance.
What is condition monitoring for machinery health
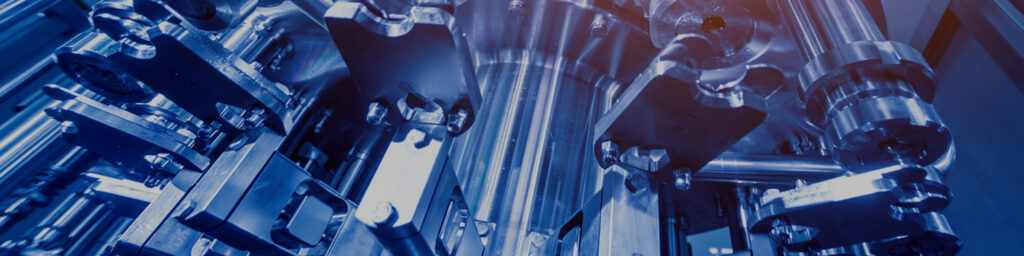
Condition Monitoring for machinery health has become a bit of a buzzword within the Industry 4.0 revolution. At its core, the term describes a series of activities that allow maintenance, reliability, and production engineers to know, at any point time, the condition of a: Single, specific machine;
Series of machines; or Complete process
Condition monitoring techniques
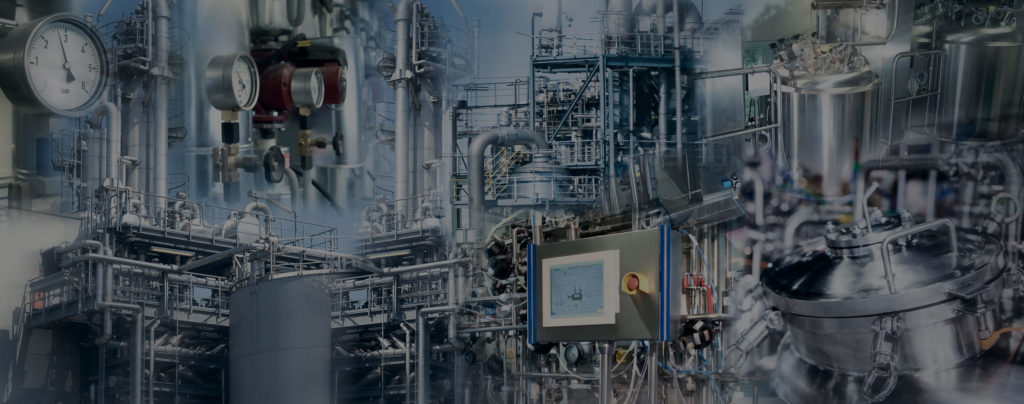
Since the dawn of industrialization, Condition Monitoring Techniques have evolved into an indispensable practice, performed at plants to safeguard the reliability and efficiency of industrial machinery, embracing technological advancements along the way. The methods used changed from visual and qualitative inspections to using hand-held devices to quantify the data — to today, where technology is available to monitor the condition of an asset anywhere in the world on a smartphone.
Wireless triaxial vibration sensors benefits – all those points in one for what?
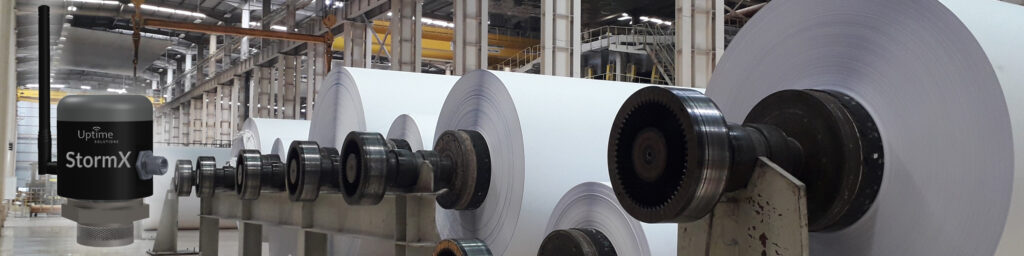
Triaxial wireless vibration monitoring sensors give you three vibration monitoring sensors in one. One sensor provides you with Horizontal, Vertical, and Axial position readings, and there is no need for cables. Sounds great! But why would you need this? What are the benefits to using wireless triaxial vibration sensors for vibration diagnostics?
8 facts to reducing spoilage with condition monitoring
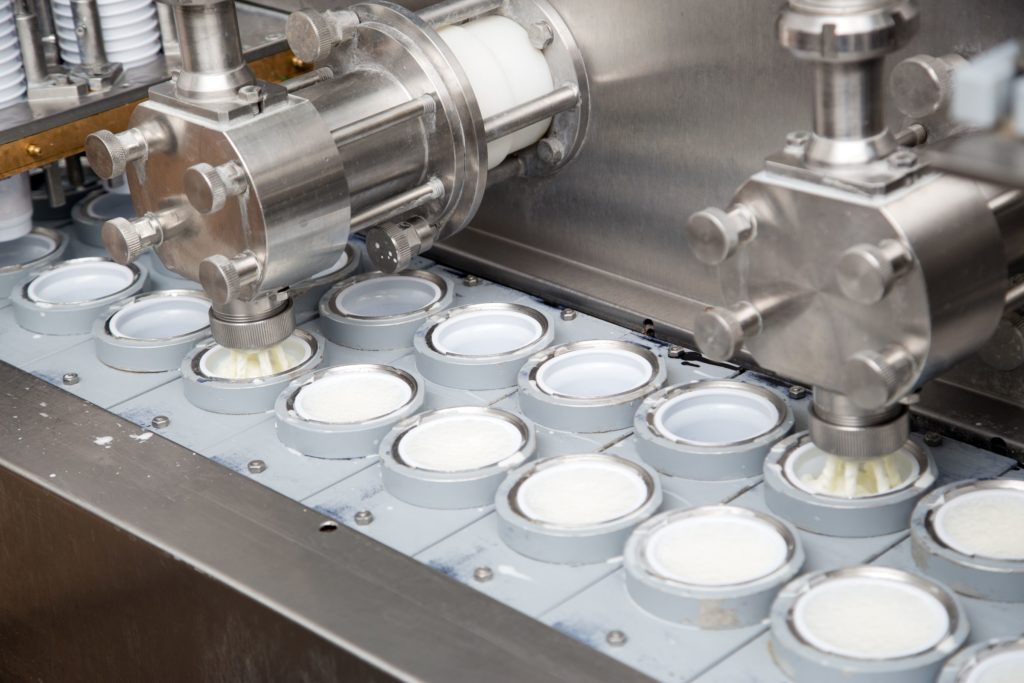
The food and beverage industry is especially vulnerable to complications when critical assets experience unplanned downtime in production facilities. It’s true. For example if an asset like an exhaust fan fails during a baking operation the temperature of the food product might not be maintained properly. This could result in waste due to losing the whole batch of product and the cost of the failure is compounded by the additional downtime to repair the disabled fan. Fortunately, monitoring machinery health (condition monitoring) can help to reduce spoilage and increase overall efficiency.
The top 10 industries harnessing the power of condition monitoring
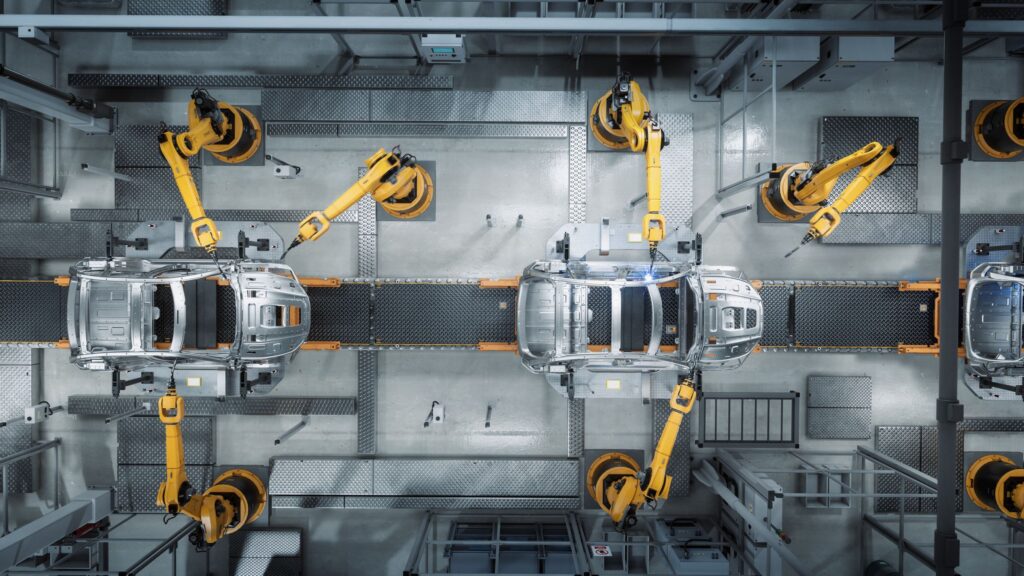
Condition monitoring has become a critical tool in the manufacturing industry as it helps companies optimize their equipment performance, reduce downtime, and ultimately improve their bottom line. By continuously monitoring the condition of critical machinery and equipment, manufacturers can detect early signs of wear and tear, identify potential failures, and schedule maintenance proactively. This helps prevent unplanned downtime, minimize repair costs, and increase the lifespan of equipment.