In today’s fast-paced manufacturing landscape, where optimizing equipment performance and minimizing downtime are crucial for staying competitive, ultrasonic sensors have become a critical component of the ultrasound condition monitoring industry. As a result, this industry has emerged as a pivotal early-detection strategy for predictive maintenance. Traditionally, vibration, temperature, and other process-oriented conditions have taken center stage in wireless condition monitoring. Until recently, ultrasound monitoring has eluded the wireless sensor market. In this article, we explore the current state of ultrasound condition monitoring in manufacturing, with a particular focus on its current applications in wireless technology and the promising directions it is headed.
The current state of ultrasonic condition monitoring in manufacturing
Condition monitoring, in its essence, involves the regular assessment of equipment health to identify potential faults and irregularities before they escalate into costly failures. Traditional condition monitoring techniques, such as vibration analysis and thermography, have long been employed in manufacturing plants. However, ultrasound technology has emerged as a game-changer, complementing existing methods and offering unique advantages.
Ultrasonic sensors: the rising star in condition monitoring
Ultrasound sensors utilize high-frequency sound waves to detect and analyze mechanical and electrical anomalies in machinery. Ultrasound condition monitoring has gained significant traction due to its versatility, non-invasiveness, and ability to detect early-stage defects that other techniques might overlook. Here are some key reasons why ultrasound has gained popularity in the manufacturing sector:
Early Fault Detection: Ultrasonic technology excels at identifying minor faults and abnormalities at their initial stages, far sooner than would be identified by traditional vibration analysis. By detecting earlier, maintenance teams have additional time to take proactive measures, especially as it relates to high-value assets or those that require a long lead time for intervention.
Remote Monitoring: The advent of wireless ultrasonic sensors have empowered manufacturers to employ remote ultrasound condition monitoring, making data collection more efficient and accessible from any location.
Versatility: Ultrasound can be applied to a wide range of machinery and components, making it suitable for diverse manufacturing industries. Ultrasound is particularly well suited to slow-speed equipment and lubrication adjustments, which typically cannot be monitored effectively through vibration.
Current applications of ultrasonic sensors in manufacturing
The integration of ultrasonic sensors technology into condition monitoring practices has brought tangible benefits to manufacturers across various sectors. Some of the primary applications of ultrasound in manufacturing include:
Bearing Condition Monitoring: Bearings play a vital role in the smooth operation of rotating machinery. Ultrasound helps early-detection of bearing faults such as lubrication issues, misalignment, and early wear, allowing maintenance teams to schedule timely interventions and prevent unexpected breakdowns.
Slow-speed Equipment: Typically, slow-speed rotating machinery below 200 rpm are difficult to monitor with vibration analysis. Ultrasound provides a bridge for this equipment, in many instances proving functional to exceptionally slow speeds of 1-2 rpm.
Lubrication: Lubrication routes have traditionally followed a time-based approach. Ultrasound has changed the game by allowing technicians to lubricate based on detected need. Ultrasound can provide feedback on both over- and under-lubricated components.
Leak Detection: Compressed air systems and hydraulic systems are susceptible to leaks that can lead to energy wastage and decreased efficiency. Ultrasonic sensors enable the quick and accurate detection of leaks, ensuring prompt repairs and optimal system performance.
Electrical Inspection: Ultrasound is utilized for electrical inspections to detect issues like arcing, corona, and tracking. Early identification of electrical faults enhances workplace safety and prevents equipment damage.
Valve and Steam Trap Monitoring: Ultrasonic sensors aid in monitoring valves and steam traps, ensuring their optimal performance and energy efficiency in manufacturing processes.
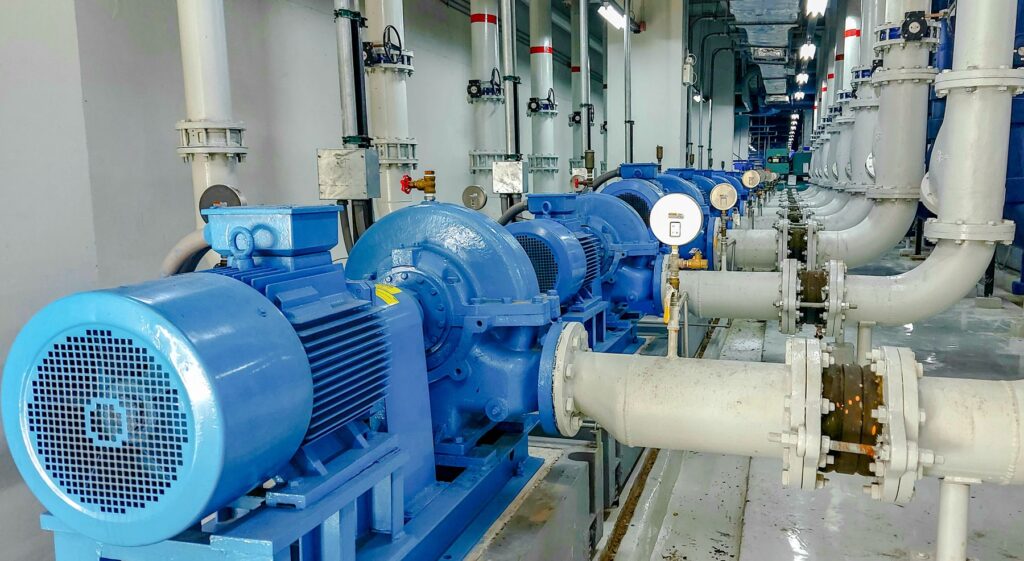
The future of ultrasonic sensors in condition monitoring
The trajectory of ultrasound technology in wireless condition monitoring appears promising. New technology in wireless monitoring now allows ultrasound to be combined with vibration and temperature monitoring to paint a more complete picture of machine health.
Integration with IoT: Fusing ultrasonic sensors with IoT platforms will enable remote data analysis and predictive maintenance. Manufacturers will leverage this connectivity to monitor equipment health regularly and make timely data-driven decisions.
Smarter Sensors: Advancements in sensor technology now allow wireless condition monitoring to include ultrasonic sensors. Capturing the ultrasound signature with audio files allows analysts to fully appreciate the data in ways never possible before from a wireless sensor.
Advancing vibration analysis: Practitioners of vibration analysis are adding ultrasound to their skill set and tools to further predictive maintenance. As wireless sensor technology becomes more advanced, so too do the skills of the profession.
Leveraging wireless ultrasound condition monitoring to maximize manufacturing efficiency
The ultrasound condition monitoring industry in manufacturing is undergoing a transformative shift, and ultrasound technology is at the forefront of this progression. With its ability to detect early-stage faults, conduct remote monitoring, and offer non-destructive testing, ultrasound has earned its place as a vital tool for maintenance professionals. As manufacturing plants increasingly adopt IoT, advanced analytics, and smart sensor technology, ultrasound’s role in predictive maintenance will continue to evolve, enabling manufacturers to achieve unparalleled levels of productivity, reliability, and operational efficiency. Embracing the potential of ultrasound technology is the key to staying competitive in the ever-evolving landscape of modern manufacturing.
Uptime Solutions' MistLX: pioneering cutting-edge ultrasound condition monitoring technology
Uptime Solutions’ MistLX unit integrates piezoelectric vibration, ultrasonic, and temperature modules into a compact wireless sensor. With exceptional sensitivity, it detects even minor machinery variations, empowering proactive maintenance to minimize downtime and expenses. The wireless connectivity enables remote access to equipment data from anywhere, while the user-friendly interface and customizable alerts cater to all expertise levels. The MistLX unit’s rugged design ensures durability in demanding environments, providing accurate and reliable performance. Combined with Uptime Solutions’ powerful condition monitoring software, it offers the greatest solution for manufacturers aiming to optimize efficiency, extend equipment lifespan, and elevate their Ultrasound Condition Monitoring practices.